Check Valves BS 1868 ASME B 16.34
Flowtorq Engineering is best manufacturer of check valves often known as non return valves. A check valve is having totally different function in comparision with other valves. Also known as non-return valve or reflux valve is a valve that normally allows fluid (liquid or gas) to flow through it in only one direction. And opposes the flow in any one specified direction. It is designed as per BS 1868, API 6D, API 594, BS 5352, ASME B 16.34, etc. standards. It consists of a swing type disc element or a lift type plug, disc or a ball as a closure member assembled inside of body, resting on the seat surface. These valves are named for their back flow prevention function. These are self operated valves, normally are actuated by reverse fluid flow either by gravity or by back pressure. Arrows are marked on valve body to indicate permissible flow direction. When the flow is towards the permitted direction, the disc or plug is raised from seating and the opening allows flow passage. When the flow is reveresed, the back flow causes the disc or plug to move to its original position and rests on the seat surface thereby preventing flow, e.i. closure of valve.
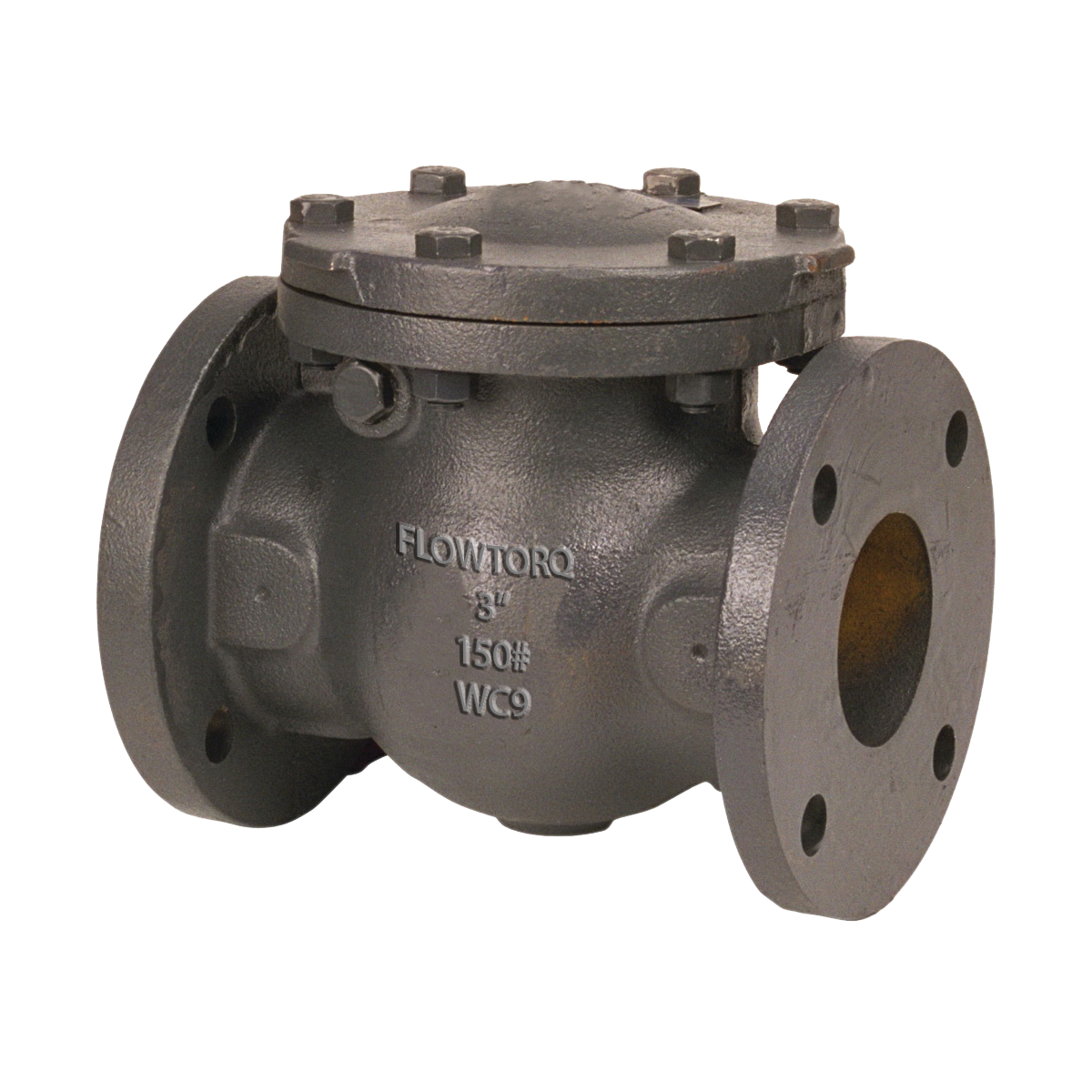
Check Valve Specifications
Cast Steel Check Valves 150# to 2500#
-
Carbon Steel - WCB, WCC
-
Stainless Steel - CF8, CF8M, CF3, CF3MÂ Â
-
Alloy Steel - WC6, WC9, WC12
-
BrassÂ
-
Bronze
-
Aluminum Bronze
-
Duplex and Super Duplex - CN7M, 4A, 6A, 5A
-
Hastelloy ad other grades - Hastelloy, Monel, etc.
-
13% Cr. Steel (Trim 1)
-
13% Cr. Steel + ST6 Stellite (Trim 8)
-
ST6 Stellite (Trim 5)
-
SS304
-
SS316
-
Inconel
-
Monel
-
All Trim as per API 600
-
Other Trim as per Client requirement
-
Flanged
-
Butt Weld
-
RTJ (Ring Type Joint
-
BS 1868
-
ASME B 16.34
-
API 594
-
BS 5352
-
API 6D
-
API 598 / BS 12266-1
-
Other End User Standards
Forged Steel Check Valves 800# to 2500#
-
Carbon Steel - A105
-
Stainless Steel - F304/L, F316/L
-
Alloy Steel - F11
-
Duplex and Super Duplex - F51
-
13% Cr. Steel (Trim 1)
-
13% Cr. Steel + ST6 Stellite (Trim 8)
-
ST6 Stellite (Trim 5)
-
SS304
-
SS316
-
Inconel
-
Monel
-
All Trim as per API 600
-
Other Trim as per Client requirement
-
Screwed / Threaded (Female)
-
Socket Weld
-
Pipe End
-
Welded Flanges
-
Welded Nipples both sides
-
Socket Weld X Threaded
-
Scoket Weld X Pipe End
-
BS 5352
-
ASME B 16.34
-
API 598 / BS 12266-1
-
Other End User Standards